Optimizing MTBF for equipment maintenance
Unplanned downtime due to equipment failures can result in substantial financial losses and disruptions to production schedules. Regular maintenance is therefore a critical aspect of any organization that relies on machinery, equipment, or assets to run its operations.
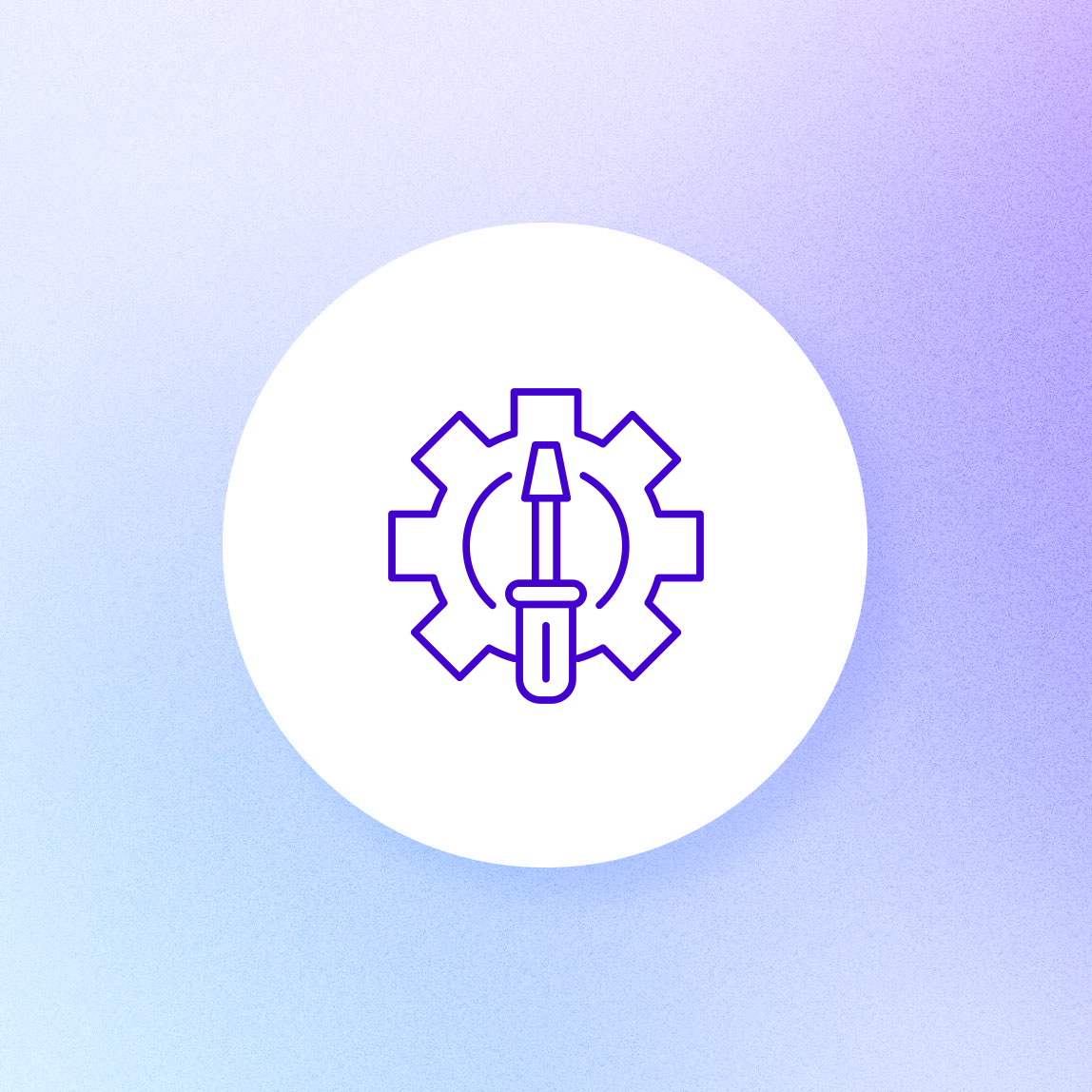
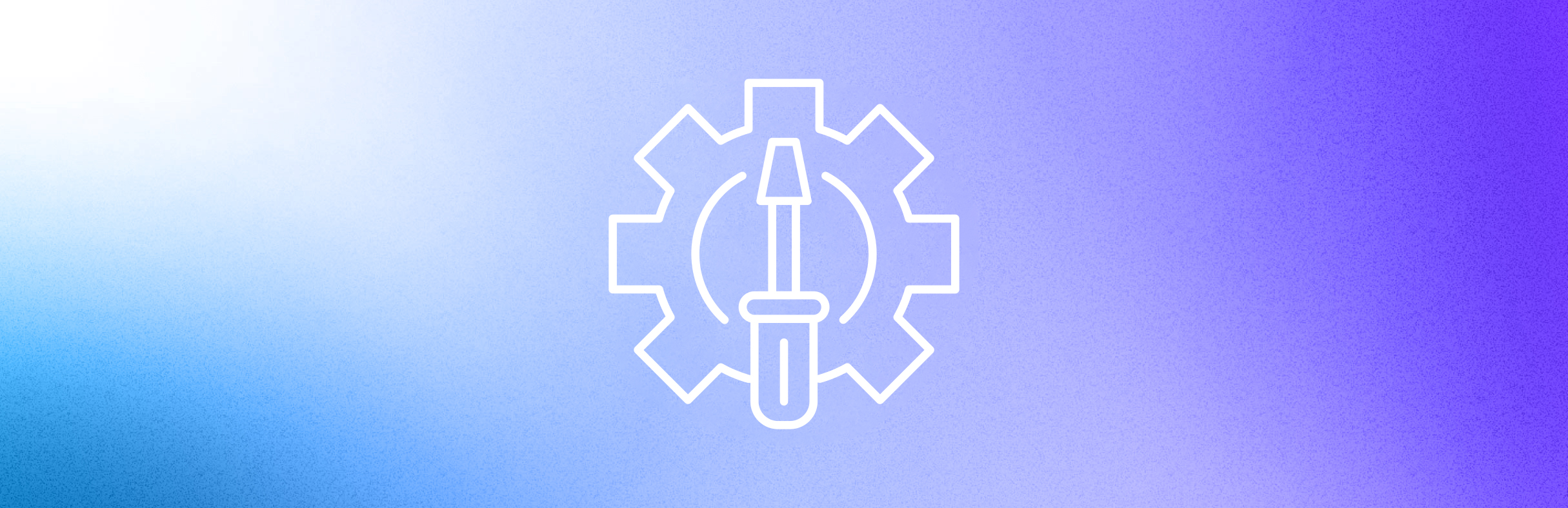
Unplanned downtime due to equipment failures can result in substantial financial losses and disruptions to production schedules. Regular maintenance is therefore a critical aspect of any organization that relies on machinery, equipment, or assets to run its operations. That's where mean time between failures (MTBF) comes into play. MTBF is a metric that plays a crucial role in maintenance planning. In this blog post, we will explore the significance of MTBF, learn how to calculate it, and understand how it can be used to plan and optimize your equipment maintenance effectively.
What is MTBF?
MTBF is a measure of the average time that an equipment or system can be expected to operate before experiencing a failure. A high MTBF typically indicates that equipment is reliable, while a low MTBF suggests that maintenance needs to be more frequent or intensive. Using this information, organizations can make informed decisions about maintenance schedules, spare parts inventory, and resource allocation.
How to calculate MTBF?
MTBF can be easily calculated by dividing the total operating time by number of failures. Let's say a conveyor system has been in operation for 1,000 hours and has experienced 2 failures during that time. The MTBF would be calculated as 1,000 hours/2 failures = 500 hours per failure. There are also tools and equipment inventory software available to automate MTBF calculations, making it easier to manage this valuable metric.
Collecting data for MTBF
Collecting accurate data that is relevant and reflects the equipment’s actual performance is essential for reliable MTBF calculations. Data sources can include equipment logs, sensor data, maintenance reports, and historical records. However, these data sources should be regularly audited to minimize errors and discrepancies and make MTBF calculations more reliable. For this, digital data logging tools can also be leveraged to automate data collection, improving accuracy and reducing manual effort.
Utilizing MTBF for maintenance planning
MTBF plays a crucial role in maintenance planning, specifically in predictive maintenance. Predictive maintenance involves using data and insights, such as MTBF, to forecast when maintenance should occur. This approach allows organizations to address issues before they result in equipment failures and costly downtime.
By knowing the MTBF of their equipment, organizations can schedule maintenance activities at optimal times, minimizing disruption to operations. This proactive approach can extend the lifespan of equipment and reduce the likelihood of catastrophic failures.
MTBF also influences the choice between preventive and predictive maintenance strategies. Preventive maintenance involves performing routine tasks, such as regular inspections and replacements, regardless of equipment condition. In contrast, predictive maintenance leverages MTBF and other data to determine when maintenance is needed, reducing unnecessary work and costs.
Challenges and considerations
While MTBF is a useful metric, it's not without its challenges. The following are some of the common concerns in using MTBF for maintenance planning:
Variability in operating conditions: Equipment may perform differently under varying conditions, making MTBF less predictable.
Incomplete data: Lack of data or inaccurate data can lead to unreliable MTBF calculations.
Complex systems: Some systems have multiple components, each with its own MTBF, making calculations more intricate.
Human error: Mistakes in data collection or analysis can affect the accuracy of MTBF values.
To address these challenges, organizations should consider factors affecting the accuracy of MTBF calculations, such as standardizing operating conditions, improving data collection methods, and investing in reliable sensors and monitoring systems. Implementing best practices for data management and analysis can help enhance the accuracy of MTBF-based maintenance planning.
Best practices for using MTBF
For effective maintenance planning using MTBF, it's essential to consider the following key factors:
Combine MTBF with other reliability metrics
MTBF is just one piece of the puzzle. Consider using other reliability metrics like mean time to repair (MTTR) to gain a more comprehensive view of equipment performance. You can also leverage insights from equipment inventory tracking software for this.
Incorporate industry-specific standards and guidelines
Different industries have unique maintenance requirements. Adhering to industry-specific standards and guidelines can help tailor maintenance planning to the specific needs of the organization.
Establish clear maintenance policies and procedures
Document and communicate maintenance policies and procedures to ensure everyone in the organization understands their roles and responsibilities.
Focus on continuous improvement
Regularly review and refine maintenance strategies. As equipment or operating conditions change, adjust maintenance plans accordingly to ensure they remain effective.
Eagle CMMS: Your partner for MTBF-driven maintenance
For organizations looking to streamline their maintenance planning and leverage the power of MTBF, Eagle CMMS can be a trusted partner. We offer equipment inventory management software powered by a range of features including real-time data tracking, work order management, preventive maintenance scheduling, and asset management. It empowers maintenance professionals to collect and analyze data effortlessly, allowing them to calculate MTBF and make data-driven decisions with ease. For more information please contact our team or schedule a demo.